Modeling Flexibility in Multibody Dynamics Simulations with Detailed Contact Analysis
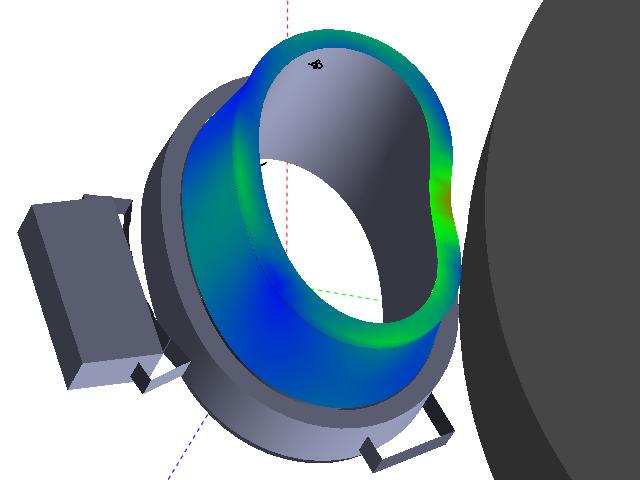
The development team of the SKF's proprietary tool BEAST acknowledged the problem when planning the introduction of the GRInding Simulation tool (GRIS). This research was motivated by the specific requirements of the new tool that are summarized below.
The requirements can be subdivided into three equally important groups. They are:
- the computational performance or efficiency
- the accuracy, and
- the potential to incorporate the analysis needed for grinding.
Efficiency
Roughly speaking, the efficiency is dependent on the number of states for the flexible body, so this number should be minimized. Besides, the flexible body model should not force the numerical solver to take smaller time steps compared to the same model with rigid components.Accuracy
Let us give a very simple example to illustrate the need for accuracy. Imagine a rotating elastic ring pressed between two plates. From the physical point of view the radial stiffness of the ring is independent of its orientation. Hence assuming the constant force acting on the ring the elastic deflection, measured as the distance between the plates, should become constant after some transient process. When simulating this in the time domain, it is important that we do not introduce vibrations due to modeling errors or numerical errors. The situation can get worse for a more complex model where small, induced vibrations can occasionally resonate with some resonance frequency of the system leading to completely unrealistic results.Analysis
In the third group of requirements one can mention distortion, due to initial stresses in the surface layer combined with uneven material removal.Flexible bodies are one of the main innovations in the GRIS tool. The project required a review of the current methods for dealing with elastic components in multibody simulation system, design of appropriate class hierarchy, analysis of possible modifications needed for the numerical solver, etc.
The results of this work are now used at SKF for parametric studies of grinding process. An article reporting some interesting aspects of the model Iakov Nakhimovski, Dag Fritzson, Mikael Holgerson:Dynamic Simulation of Grinding with Flexibility and Material Removal was presented at Multibody Dynamics in Sweden II seminar in November 2001.
We plan to submit another paper describing our model of internal stress release during grinding to an international journal within a few months.
Contact: Iakov Nakhimovski,
iakna@ida.liu.se
Page responsible: Webmaster
Last updated: 2012-05-07