Quality Function Deployment
* Methodology for defining the customer's desires in the customer's own
words, prioritizing these desires, translating them into engineering
requirements, and establishing targets for meeting requirements.
Tool for defining the "right" problem to solve.
-Developed in Japan in
1970's - Mitsubishi & Toyota
-Introduced in US in 1980's (Hauser and
Clausing, Harvard Business Review, May-June 1988).
*Also known as:
-Voice of the Customer
-House of Quality
-Customer-Driven
Engineering
-Matrix Product Planning
*Uses a series of matrices to structure information acquisition and
documentation.
QFD Matrices
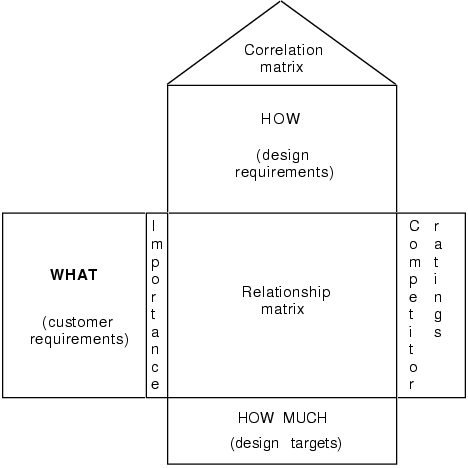
Figure 1.
General organization of a QFD matrix.
QFD Methodology
1. Identify customers (both internal and external).
2. Create a list of
customer requirements (WHATS).
* Record customer responses to the question: "What are the important
(qualities, characteristics, elements, features) of _____________?"
* Record
in customer's own words - "Voice of the Customer."
* Categorize
hierarchically (primary, secondary, tertiary,...).
3. Prioritize the customer requirements on a scale of 1-5.
4. Compile
list of design requirements (HOWS) necessary to achieve the market-driven
whats.
* Each requirement should be quantified.
* Arrows show direction for
improvement (up for increasing, down for decreasing, etc.)
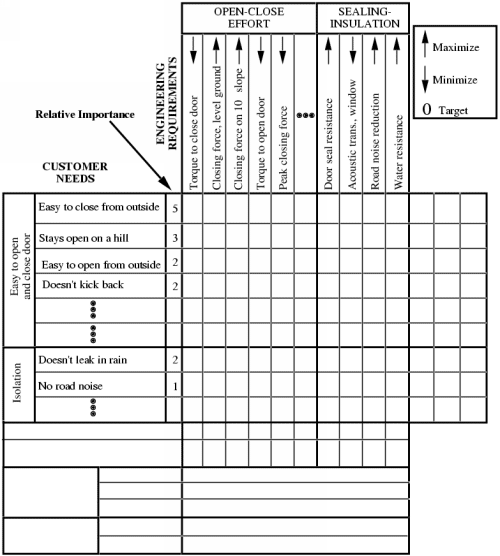
Figure 2. Start
with WHATs and HOWs.
5. Determine relationship of design requirements to customer requirements.
* Cell strengths quantify the importance of each HOW to achieving each
WHAT.
Strong
relationship
Some
relationship
Weak
relationship
No mark for no
relationship
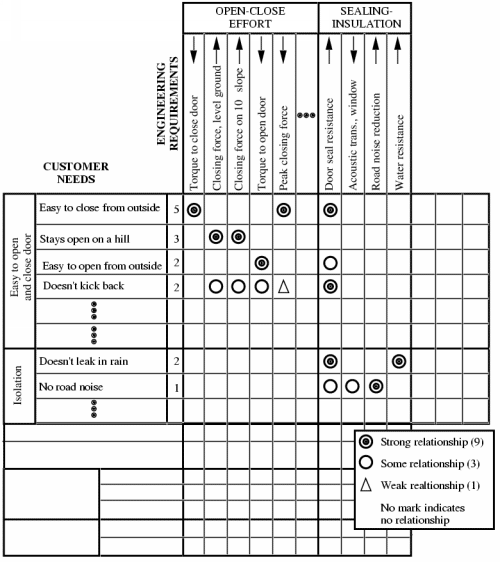
Figure 3. Adding
correlations between WHATs and HOWs.
6. Determine how the customer perceives competitors' abilities to meet
requirements.
* Competition benchmarking.
* Rate competitors on a scale of 1-5 with
respect to each customer requirement.
7. Rank the technical importance of each design requirement.
* Absolute rank is total of relationship value (quantify step 5
relationships) times customer importance ranking.
* Relative importance is
based on assigning ordinal ranking to each design requirement based on absolute
rank (from previous step).
8. Rate the technical difficulty of each design requirement so design team
can focus on the important/difficult HOWS.
9. Establish correlation matrix
(roof of House of Quality) to determine interrelationships of design
requirements.
Strong positive
interaction
Positive
interaction
Strong
negative interaction
Negative interaction
10. Determine target values for the design requirements (HOW MUCH).
11.
Areas that require concentrated effort are identified. Key elements are
identified for follow-up matrix development. Assessment of technical difficulty
and importance are useful in identifying these elements.
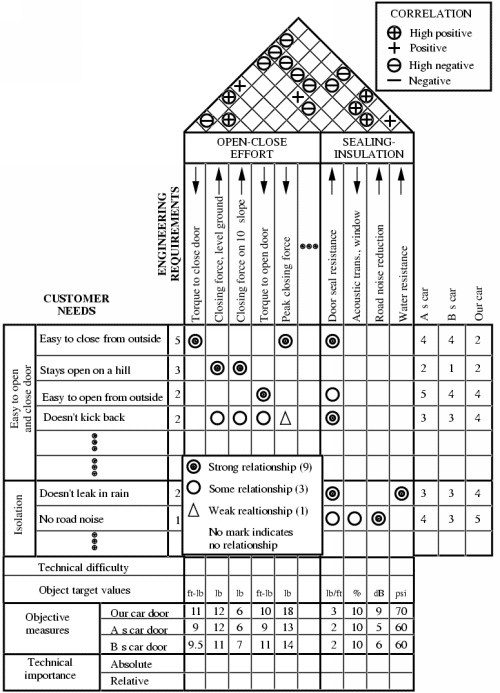
Figure 4. QFD
matrix with objective measures added.
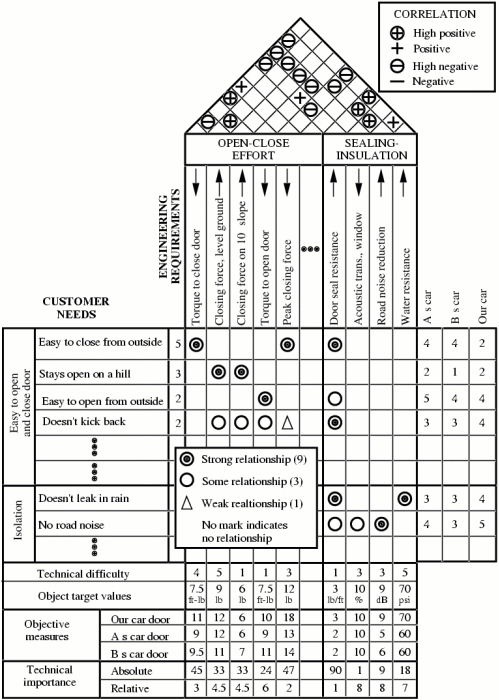
Figure 5.
Completed QFD matrix.
QFD: Summary
* The importance of QFD:
- Provides a framework for upfront planning and product development.
-
Uses multi-functional teams to enhance design and decision-making.
- Promotes
teamwork (necessary for Concurrent Engineering).
- Maintains customer ideas
and requirements, in the customer's words, throughout the process.
* Engineered products adhering to customer wants result in customer
satisfaction.